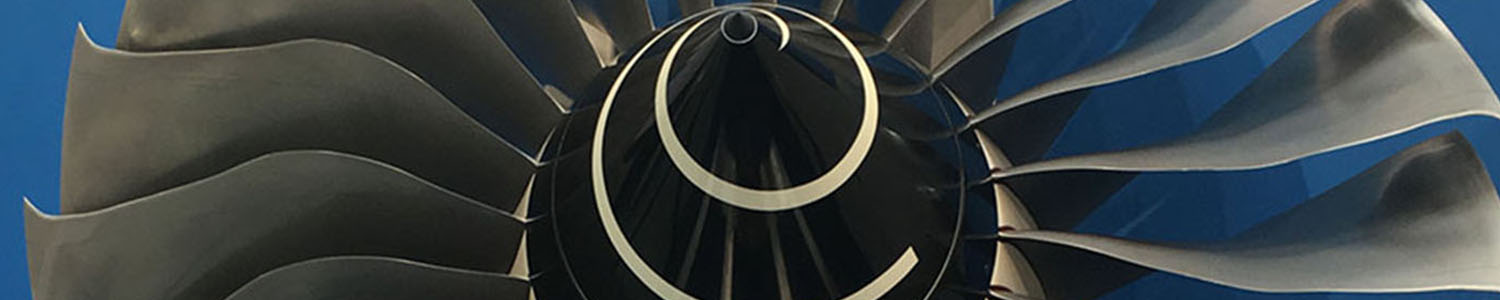
Aerospace Industry
In a very buoyant and competitive market, where the main OEM’s demand cost savings from their supply chain on a continuous basis, companies have no other option but to focus on process innovation and optimisation to become more productive. This is the point at which we get involved.
Kyocera SGS is a leading manufacturer of high performance carbide cutting tools in the Aerospace industry. You will find our tooling used in manufacturing many parts of a modern jet engine.
Demanding tight tolerances and exceptional surface finishes, components for the aerospace sector can be listed in three main areas: Airframe; Engine; and Landing Gear.
Airframe components such as ribs and spars are typically produced from aircraft grade aluminium and the milling of these components often involves removing a large volume, over 90%, of the raw billet. So, high efficient machining at high speed is required to reduce the cost and keep up with customer demands.
While the ‘cold’ side of the modern jet engine uses both metallic and non-metallic materials including aluminium and carbon fibre reinforced composites, the ‘hot side’ requires the ability to reliably machine heat resistant super alloys (HRSA) such as Hastelloy, Inconel, Waspaloy, Rene alloys, Haynes alloys, Incoloy, MP98T, TMS alloys, and CMSX single crystal alloys. With these ‘difficult to cut’ materials achieving the required tool life and machining efficiencies takes knowledge and experience, and we have helped numerous customers attain machining cycle times that seemed impossible.
Required to hold the complete weight of the aircraft during take-off and landing, the strength requirement of the Landing Gear has many years restricted the material choice to highly processed steels. While the aircraft industry has searched for tougher steels with the reliability needed to reduce the weight of landing gear, it has in parallel also introduced alternatives such as titanium and Polymer Matrix Composite (PMC) materials.
Our tooling commonly used in Aerospace manufacturing
For casing work, disks and blisks and shaft work
We recommend our Combination Tooling.
Ideal for drilling and milling parallel, swage holes and counterbores. Our combi-drill solution offer a reduction in the number of tools required for each hole. The drilling of stepped holes and chamfers can now be combined into one tool that delivers a stable, accurate process that reduced both cycle times and tooling costs.
Blisk and Blade Manufacturing
We recommend our Taperball nose and barrel tooling which are optimised solutions for 3D forms, in materials such as titanium.
LP Fan Disk
SGS developed tooling and processes used on next generation turbo fan engines. The fan disc slot form tool (bulb tool) is used to machine the finished slot form.
Aluminium Aerospace Components and our Solutions to Manufacturer
Majority of Aluminium parts in aerospace are large in size (up to 16 metres long) and require up to 90% volume machined away.
They generally have thin walls and floors and tight corners so good surface finish is essential.
SGS has developed a range of tooling especially for machining Aluminium. Our Advanced Productivity Rougher (APR) and Advanced Productivity Finisher (APF). This range comes in 3 flute and 4 flute options with long reach up to 5xD protrusion.
SGS has also developed a tooling range with PRW and PRB geometry. Ideally suited to suppress vibration and impose surface stability. These tools are used for machining the annulus filler and SGV tooling in aluminium.
What we do for our Customers
The Manufacturing Challenge
How to manufacture parts in less time? How to reduce scrap levels? How to become more profitable? These are some of the issues we face with our customers on a regular basis.
Identifying and anticipating our customers’ needs and requirements is what our group of engineers do in order to formulate solutions that allow us to satisfy their needs effectively.
Once the objectives and expectations are set, is the time to apply our knowledge and expertise to begin generating those savings and benefits our customers need to stay competitive in the market place.
Focus on 97% of the Machining Equation
KYOCERA SGS is focused on the most cost effective solutions at the spindle to produce the highest quality parts in the shortest amount of time. This is achieved through our commitment to performance, quality and consistency, combined with an outstanding service.
Remember that only 3% of the machining cost is represented by the tooling. However, when the right tooling, combined with tool path and machining strategy optimisation, the right tool holding and fixturing device, it can deeply impact the other 97% of the machining equation.
This is what we do at KYOCERA SGS. We provide a holistic approach aimed at impacting your productivity.