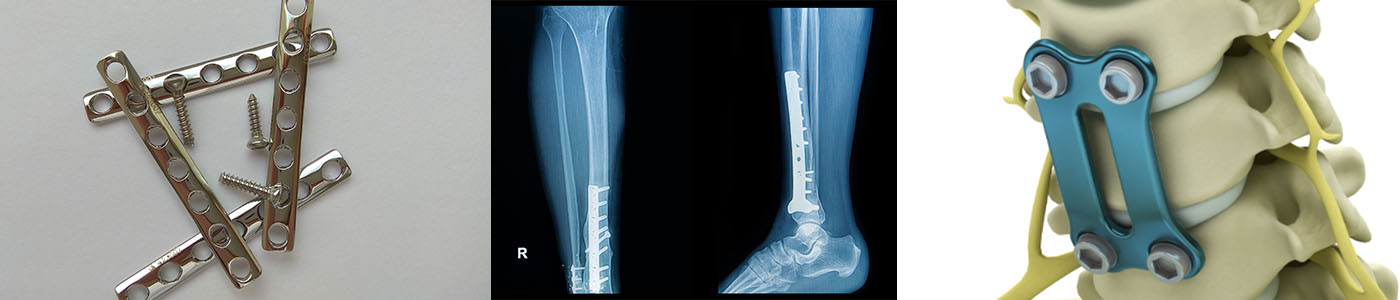
Trauma and spinal Components & Solutions
Components
Trauma plates come in many shapes and sizes and are manufactured from biomaterials such as titanium, various stainless steels and cobalt chrome. Plates for fractures are designed to follow the natural contours of the bone and are screwed into place holding the bone pieces together whilst they heal. Spinal plate implants are manufactured from the same materials and are designed to decompress and stabilise the spine. SGS has a full range of high-performance end mills and drills well suited to the machining of these complex components.
Solutions
The variety and complexity of design of trauma and spinal plate components dictates that multiple tooling solutions and strategies are employed when machining them.
SGS has developed comprehensive range of milling cutters and drills suitable for producing these titanium, stainless steels and cobalt chrome plates.
In addition, we have developed special tooling including high-feed tools, and our patented combi-tool solutions.
Milling of trauma plate components
SGS have a range of 3, 4, 5, 6 and 7-flute tooling solutions suitable for slotting, profiling and dynamic milling of difficult-to-machine materials such as titanium, cobalt chrome and stainless steels.
Working with major medical implant manufacturers we have adapted and refined our high-performance range of tooling to ensure that cutting data is maximised whilst simultaneously increasing tool life.
V-Carb milling solution
SGS’s V-Carb solution is ideal for profiling and finishing of difficult medical materials.Our 5-flute design also makes it suitable for trochoidal / dynamic machining strategies. As with all SGS’s high-performance tooling the
V-Carb range has a variable geometry design for vibration reduction. The V-Carb range is available in stub, regular and long flute lengths, and also with a ball-end version ideal for scanning.
Drilling of titanium and cobalt chrome
SGS has a range of high-performance drilling solutions including our Hi-PerCarb and through-coolant ICe-Carb ranges. The Hi-PerCarb drill features a double margin design that can remove the need for reamers, whilst other design features are engineered to maximise chip control, drill strength, penetration rates, and therefore productivity.The ICe-Carb Series 140 drill features an internal coolant design that allows for better control of machining temperatures and chips when machining materials such as titanium. The ICe-Carb drills design features reduce cutting loads, increase operating parameters and enhance tool life.
Hi-PerCarb drill solution
Features such as a double margin, secondary flute, and Specialized 145° notched point give the Hi-PerCarb drill the ability to maximise chip control and penetration rates. A self centering point geometry can also eliminate the need for
spot drilling. The Hi-PerCarb drill range is available in 3xD and 5xD versions and in Metric, Fractional, Letter and Number sizes and in diameters Ø0.40mm to Ø16.0m.