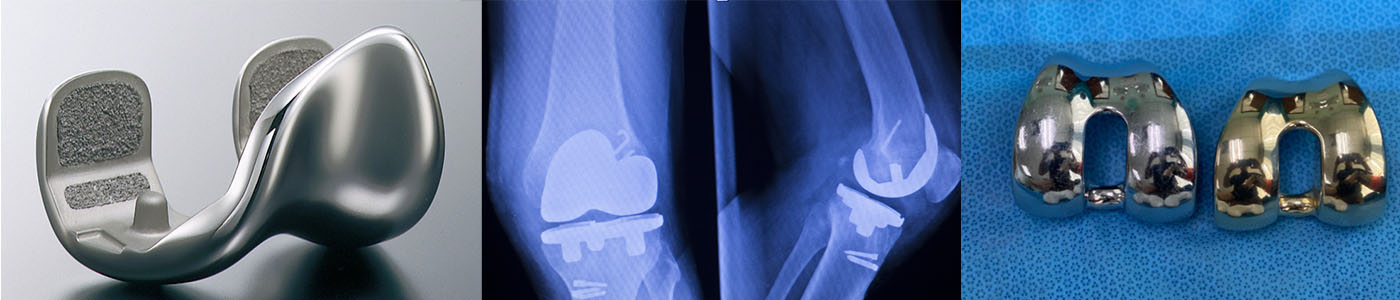
Femoral Knee Components & Solutions
Components
Femoral knee replacement parts mimic the natural shape of the joint and are usually made from cobalt chrome and 17-4 PH stainless steel.
Due to the tight tolerances and surface finishes required, femoral parts are usually machined on 5-axis grinding machines. However, this process can generate high temperatures that may distort the metal and lead to scrapped parts.
The drive for more efficient, stable and cost-effective manufacturing processes has in recent years seen medical manufacturers start to move towards milling solutions.
The challenge when milling is to achieve a burr-free profile with superior surface finish that minimises the need for linishing and manual polishing, and at the same time maximises productivity and tool life.
Solutions
SGS has a comprehensive range of off-the-shelf high-performance tooling with geometries well suited to the machining of cobalt chrome and 17-4 PH stainless steel.
In addition, we have developed specific tooling solutions for various areas of femoral components, including taper ball end cutters for box and cam sections, and barrel cutters for the main condyle surfaces.
Milling Condyle surfaces- Barrel tools
The condyle surfaces represent the largest portion of cycle time when machining femoral components. These surfaces have traditionally been milled with ball nose cutters using a scanning strategy.
Whilst this strategy delivers the required surface finish, the small step overs result in an unsatisfactory cycle time. The SGS range of barrel tools have achieved step overs of up to 3.0mm and a feed rate of over 800mm/min whilst still delivering surface finishes within tolerance.
Milling box section feature – Taper ball nose tools
The box section feature of femoral components present challenges when milling due to deep walls, small corners and high surface finish requirements that minimise manual polishing.
SGS’s tapered ball end tool solutions benefit from our patented vibration-reducing geometries that deliver the required component surface finishes, whilst our choice of carbide and coatings help to maximise tool life.