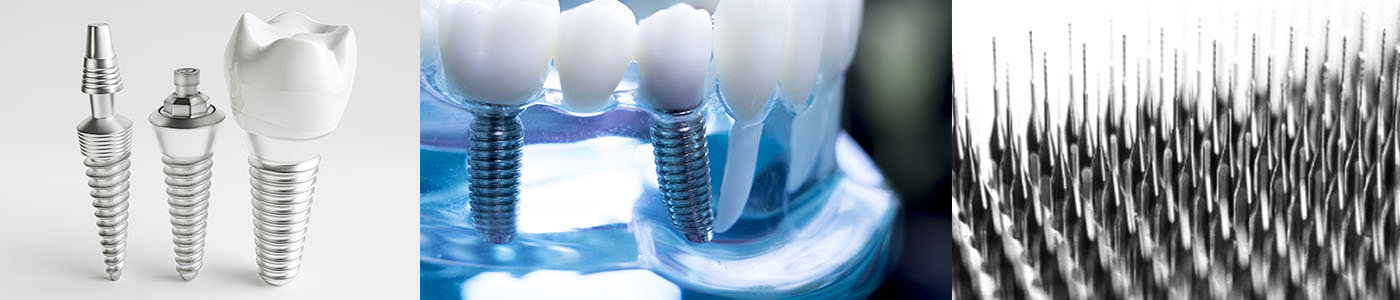
Dental Implant Components & Solutions
Components
Dental implants generally consist of three parts, the implant, the abutment and the crown. Additionally, dental work may also include the fitting of bridges and bars.
The Implant
The implant is a small titanium screw that is positioned into the jawbone beneath the gum and acts as an artificial root. The implant serves as a base for fixing individual ‘teeth’ or a multi-tooth bridge.
The Abutment
The abutment connects the implant to the crown and can be made from several materials such as titanium and zirconia.
The Crown
The crown is the replacement tooth and is the only part you see in the mouth. Screwed directly into the abutment, crowns can be made from a variety of metals and composites, including porcelain, ceramic, acrylic, or metal alloys.
Bridges and Bars
Support several replacement teeth and are produced from materials such as titanium and zirconia. The components are customised to suit the individual’s mouth.
Solutions
By their very nature dental implants tend to be small, complex and customised to suit the individual’s mouth, and therefore require multiple small/micro tooling solutions and strategies to be employed when machining them.
SGS’s range of high-performance end mills and drills are available in sizes as small as Ø1.0mm and have the same design features as our larger tools, including variable pitch, helix and rake angle, all aimed at reducing resonance, vibration and chatter, the main cause of premature tool failure.
In addition, SGS has developed a comprehensive range of micro end mills suitable for producing these titanium, cobalt chrome and zirconia components.
Our micro tool range starts at Ø0.1mm and is available in both square and ball end solutions and in various cut lengths up to 12xD.
Milling of dental implants
SGS has a comprehensive range of high-performance end mills suitable for machining these small complex components. Our range of tools start as small Ø0.1mm and has the same design features as our larger tools including variable pitch, helix and rake angle. All these design features are aimed at maximising metal removal rates, thus reducing cycle times, therefore improving productivity.
Z-Carb milling solution
With the introduction of the patented Z-Carb range of tools back in 2000, SGS became the first cutting tool manufacturer to launch variable geometry tooling on to the market.
The launch of the Z-Carb AP range with its patented variable rake geometry further improved the tool’s ability to maximise metal removal rates, thus reducing cycle times, and therefore improving productivity. In subsequent years SGS have added several variants to the Z-Carb family, creating one of our most comprehensive ranges. The Z-Carb range is available in sizes as small as Ø1.0mm and has the same variable design features as our larger tools.
You can read more about our Z-Carb range here:
Micro tool milling solutions
In recent years SGS have turned attention to the micro tool market and introduced a comprehensive range of highperformance quality tools. During an extensive testing and development process we identified advanced geometries that extend tool life, reduce chatter, cut cycle times and improve part quality. We also identified a coating that not only gives these micro tools a 250% life increase over the competition but increases chip flow even in low RPM applications.
Our specially selected substrate is inspected at our in-house metallurgical lab prior to manufacturing to ensure only the highest-quality carbide is turned into your precision micro tool. Our micro tool range includes both metric and fractional square and ball end products and is available in diameters from Ø0.1mm to Ø3.0mm, and in various cut lengths up to 12xD.
We believe that these tools, albeit small, are a huge step forward for micro machining.
You can read more about our micro tool range here.
Or you can download our brochure here: